Project Sponsor
The Boeing Company
Clients
Amanda Nemec - Senior Engineering Manager at Boeing
Michael Vogelsang - Mechanical Design and Analysis Engineer at Boeing
Reed Esper - Structural Analysis Engineer at Boeing
Project Description
The Boeing Drone Project is created to analyze and optimize a surveying quad copter drone that is still in its early stages of design. This project was specifically created to enhance the current weight and flight time of the existing drone from Boeing. The purpose of the drone is to surveillance the large plots without a worry of losing contraption to battery depletion. The team is expected to have a 3D printed drone body to perform the task under the requirements of the clients. The client requirements are weight reduction, flight time, and thurst to weight ratio, strength, lift and drag, and space provision for mounting the pre-purchase equipments. Some of pre-Purchased parts includes Jetson Nano GPU, pixhawk PX4 flight controller, LiDAR, PM07 power management board, Arducam IMX477 PTZ camera and gimbal. To achieve the goal the team is using several softwares such as Solidworks for Designing, ANSYS for stress tests, and eCalc Multi-copter for flight duration and power draw.
Requirements and Goals
Original Drone Design
The first ever drone design was created by Reed Esper, last year their team made a heavy but sturdy drone that is capable of flying with minimal components. The structure of the original drone resembles a basic, camera-mounted quadcopter drone. The camera for surveying is mounted on the underside of the body while a Lidar was attached to the top. With the four blades, there also comes 4 motors at the end of each arm. The landing gears are two āDā shaped legs which can absorb a large impact upon landing but add lots of weight to the drone body. All other components like the battery and transceiver were attached to the front of the body.
The images of the originial drone are displayed below.
Original Drone Performance
The original drone was quiet heavy (4.02lbs) and and had a low thurst to weight ration (1.81). The drone was capable of lifting up and down but the lateral movement was restricted. Landing of the drone did not appear to be agile but due to the design of the landing gears it appears to absorb the major shocks on the ground.
To view detailed performace of original drone:
Final Design
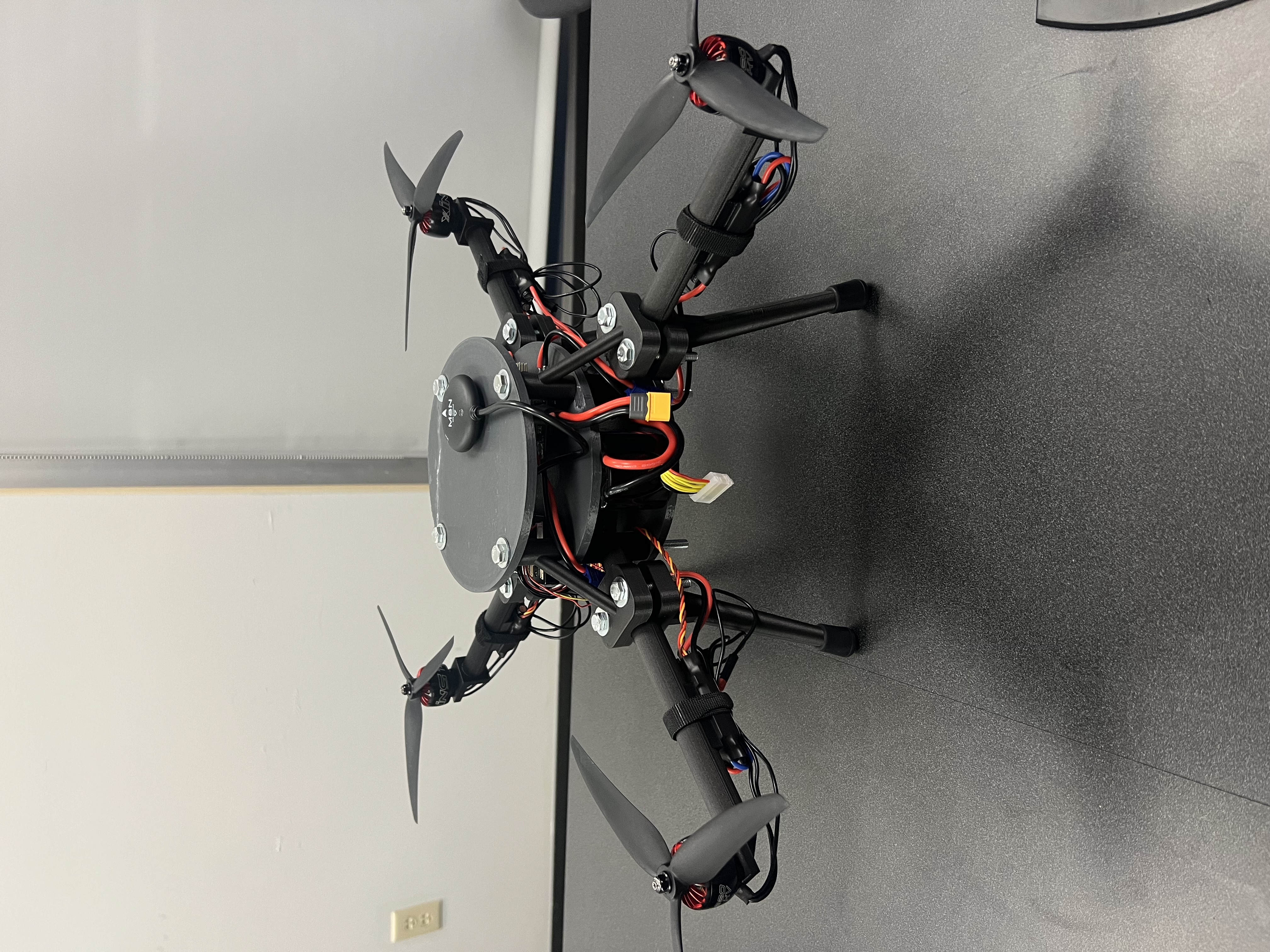
The final prototype is made up of Onyx Polymer and ABS. The prototype consists of 3 discs, 4 legs, 4 arms, 4 upper brackets. All other parts are 3D printed. The were manufactured from hubs.com (outsourced). Total weight of the prototype is 2.2lbs (after attaching all 3D printed parts with bolts). The top disc is attached to middle disc with upper truss which then connected to the lower disc with arms. Finally, legs were attached to the arms with lower truss to upper truss. The list of other equipments and parts attached to it for manual flight is listed below:
Part Description | Pcs. | Material | Weight | Cost | Manufactured |
---|---|---|---|---|---|
Arms W/Spacers | 3 | ABS | $214.67 | Hubs | |
Legs W/Arm Clamps | 3 | Non-reinforced Onyx | $260.08 | Hubs | |
Spacers W/Arm Clamps | 3 | Non-reinforced Onyx | $117.52 | Hubs | |
Discs W/Key | 3 | Non-reinforced Onyx | $75.68 | Hubs |
Component | Quantity | Company of Purchase |
---|---|---|
Hobbytown 40A ESC | 4 | Hobbytown |
Gemfan 9045 3-Blade Prop | 4 | getfpv |
Battery Charger | 1 | Amazon |
Battery Connector | 1 | Amazon |
Socokin 6S Lipo Battery | 1 | Amazon |
iFlight XING 2814 880KV Motor | 4 | PilotHQ |
Pixhawk PM07 Power Module | 1 | getfpv |
Flysky FS-i6X 2.4GHz RC Trans/Receiver | 1 | Amazon |